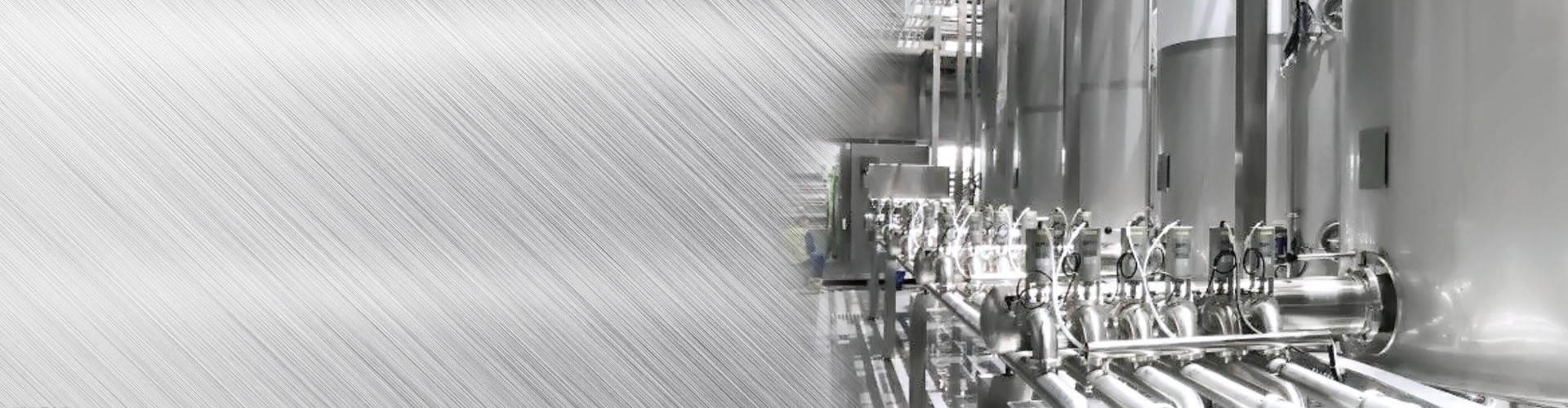
Microbial fermentation tank is a type of equipment widely used in biotechnology, pharmaceuticals, food processing, and chemical industries. It is mainly used to cultivate microorganisms (such as bacteria, yeast, mold, etc.) or cells, and produce specific products through the fermentation process, such as antibiotics, alcohol, enzyme preparations, organic acids, biofuels, etc. The design and operation of fermentation tanks involve knowledge from multiple disciplines such as biology, chemical engineering, and automation control.
Here are some key features and components of microbial fermentation tanks:
Structural composition: The fermentation tank usually includes the following parts:
• Tank body: Provides a closed space for microbial growth, mostly made of stainless steel, ensuring a sterile environment Stirring system: equipped with a stirrer for mixing culture medium and microorganisms, increasing dissolved oxygen, promoting mass and heat transfer.
Ventilation and oxygen supply system: By introducing sterile air or oxygen into the tank, the oxygen supply required for microbial growth is ensured.
Temperature control system: Maintain a constant temperature inside the tank, suitable for the optimal conditions of microbial growth.
PH control system: Automatically adjust the pH value of the culture medium by adding acid-base regulators.
Feeding and sampling ports: allow for supplementing nutrients or taking samples for testing during the fermentation process.
Pressure control system: maintains the pressure inside the tank, especially for certain fermentation processes that require high-pressure operation.
Operation mode: The fermentation process can be batch, continuous, or flow addition (semi continuous), and each mode is suitable for different production needs.
Monitoring and Control: Modern fermentation tanks are equipped with advanced sensors and automated control systems, which can monitor and control key parameters such as temperature, pH, dissolved oxygen level, pressure, etc. in real-time during the fermentation process, ensuring efficient and stable production of target products.
Sterilization and aseptic operation: The fermentation tank needs to undergo strict sterilization treatment before and after use. Common methods include moist heat sterilization (such as high-pressure steam sterilization) and chemical disinfection to prevent contamination by bacteria.
Product recovery: After fermentation, the target product is recovered from the fermentation broth through separation and purification steps such as centrifugation, filtration, and extraction. The development of microbial fermentation tank technology is continuously driving the progress of the biological manufacturing industry, which is of great significance for the production of efficient and environmentally friendly biological products.
Microbial fermentation tank technology is a core application technology in the field of biotechnology, which combines multiple disciplines such as biotechnology, chemical engineering, and automation control, aiming to efficiently and controllably carry out microbial fermentation processes.
Here are some key technical aspects:
1. Stirring and mixing technology: Fermentation tanks are usually equipped with mechanical stirring devices, including stirring shafts and different types of stirring paddles (such as turbine paddles, anchor paddles, propulsion paddles, etc.), to promote liquid flow and mixing, ensure full contact between microorganisms and nutrients, and increase dissolved oxygen. The selection of stirring speed and blade type is crucial for the fermentation effect.
2. Ventilation and dissolved oxygen control: Providing sufficient oxygen for aerobic microorganisms is the key to successful fermentation. The fermentation tank adopts a ventilation system, which introduces air or pure oxygen through sterile air filters, and disperses the gas into small bubbles through methods such as microporous aeration and jet ventilation, increasing the gas-liquid contact area and improving the dissolved oxygen efficiency. The dissolved oxygen (DO) sensor monitors the level of dissolved oxygen in the tank in real-time and automatically adjusts the ventilation volume.
3. Temperature and pH regulation: The temperature and pH value during the fermentation process directly affect the growth of microorganisms and product synthesis. The fermentation tank is equipped with a precise temperature control system, such as an electric heating sleeve or cooling coil, as well as a pH automatic control system, which automatically adjusts by adding acidic and alkaline solutions to ensure that environmental conditions are always within the optimal range.
4. Feeding and emission strategies: In order to extend the fermentation cycle or increase product concentration, a flow addition feeding strategy is often adopted to timely supplement nutrients. Meanwhile, by overflow or continuous discharge, the concentration of inhibitors in the fermentation broth is controlled to maintain a good fermentation state.
5. Sterilization and aseptic operation: The fermentation tank and its associated pipelines need to undergo strict sterilization treatment before use, such as high-temperature and high-pressure steam sterilization, to ensure a sterile environment. The tank design, material selection, and sealing technology must all comply with sterile standards.
6. Automation and intelligent control: Modern fermentation tanks are integrated with advanced automation control systems, including PLC, SCADA systems, etc., to achieve full monitoring and precise control of the fermentation process. By utilizing big data analysis and machine learning techniques, fermentation conditions can be optimized, potential problems can be predicted and solved, and production efficiency and product quality can be improved.
7. Product separation and purification technology: After fermentation, the separation and purification of products are equally important, including various technologies such as centrifugation, filtration, chromatography, membrane separation, etc., to obtain high-purity target products.
In summary, microbial fermentation tank technology is a highly comprehensive technical system that promotes the development of biological manufacturing towards more efficient, environmentally friendly, and intelligent directions through continuous technological innovation and optimization.
The installation and debugging of microbial fermentation tanks are important steps to ensure the smooth progress of the fermentation process and achieve the expected yield. The specific steps are roughly as follows:
Preliminary preparation and inspection: • Location determination and infrastructure construction: Select a suitable installation location based on the size and equipment specifications of the fermentation tank, and prepare basic materials according to the design drawings, such as pouring concrete foundations.
Equipment inspection: Before installation, conduct a comprehensive inspection of the fermentation tank to confirm that there is no serious deformation, damage, or missing parts. Check if all connecting threads are intact, and conduct a no-load trial run of the mixer to ensure that the transmission components are functioning properly.
• Tank installation and fixation: • Place the fermentation tank on a pre prepared foundation and secure it firmly with bolts. The fixing method usually uses buried bolts underground or directly fixed on the foundation to ensure the stability and level of the tank body.
• Attachment installation and connection: • Install inlet and outlet, ventilation system, electrical control system (including motor, controller, instrument, etc.), ensuring that all pipelines are tightly connected and leak free Perform functional testing on electrical equipment to ensure circuit safety and reliability, while checking that all pipelines are unobstructed.
• Instrument calibration: • Calibration of instruments on the tank body (such as thermometers, pH meters, dissolved oxygen meters) to ensure accurate readings, which is crucial for monitoring the fermentation process.
• Sealing test: • Test the sealing of the entire fermentation system, especially at the inlet and outlet, ventilation openings, etc., to prevent external microbial contamination or internal medium leakage.
Debugging and trial operation: Conduct a trial operation of sterile water or simulated media, check whether the functions of stirring, heating, cooling, ventilation, pH and dissolved oxygen control are working properly, and make minor adjustments based on actual operating data Observe and record the operation status of the equipment to ensure that all control systems respond sensitively and operate stably.
• Safety inspection: After installation and commissioning, conduct a comprehensive safety inspection, including electrical safety, mechanical protection, emergency stop function, etc., to ensure compliance with safety regulations.
• Training operators: • Provide systematic training to operators, including equipment operating procedures, maintenance knowledge, and emergency response measures, to ensure that they are proficient in using fermentation tanks. Through the above steps, ensure that the microbial fermentation tank can be safely and efficiently put into production, and achieve the expected fermentation effect.
Shanghai Beyond Machinery Co., Ltd.
Beyond Machinery specializes in the design and manufacturing of fermentation tank. Please contact us now, and our professional technical engineers will customize the equipment plan for fermentation tank and provide a quotation. Please contact us now to obtain the latest equipment plan and quotation.