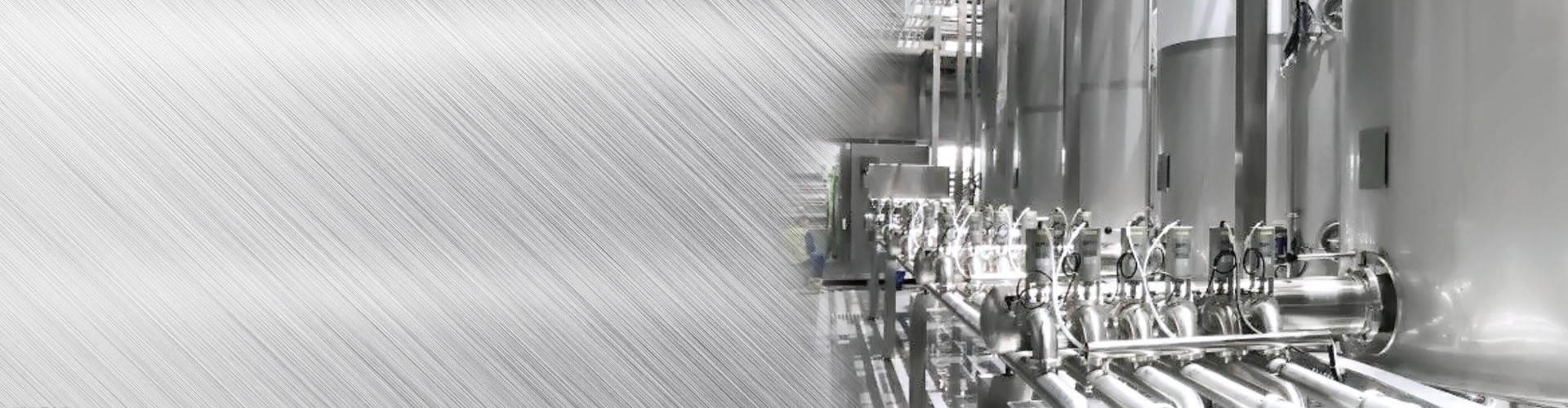
1 Introduction
In recent years, the level of labor wages in China has significantly increased. Compared to the past decade, labor costs have doubled, and the labor advantage of China's manufacturing industry is gradually weakening. The labor force group is undergoing intergenerational replacement, and the difficulty of recruitment has become an increasingly prominent contradiction between labor supply and demand. We are in a new era of leapfrog development from "manufacturing" to "intelligent manufacturing"; And if the sugarcane plant cell water extraction process production line is manually operated, it has defects such as large fluctuations in heating steam source, poor balance of steam, water, and materials, concentration ratio relying solely on experience judgment, unstable parameter control, or shutdown, low production efficiency, and easy to cause fluctuations in the quality of sugarcane plant cell water, which is not conducive to the large-scale and balanced production of sugarcane plant cell water, It is also not conducive to ensuring the quality and taste of sugarcane plant cell aquatic products. Therefore, achieving automation of the sugarcane plant water extraction production line is a necessary condition for the success of the project.
This paper is to study the application of automatic control system in the production process of sugarcane plant water extraction, and develop a distributed automatic control system based on fieldbus and Industrial Ethernet to realize the stable and controllable parameters of steam source for heating, and the whole process automatic control of the production process of constant pressure and constant flow transportation of Sugar cane juice, drainage and bottom drainage of tank body, and quantitative proportion of sugarcane plant water, so as to achieve the industrialization goal of 40 tons of water per day.
The sugarcane plant water beverage production workshop is divided into six main sections, namely raw material extraction, primary heating, pre physical filtration, secondary heating, membrane filtration, and sugarcane plant water blending. These six sections put forward their respective control objectives, which can be summarized as: material balanced transportation, Dynamic equilibrium of pressure, temperature and flow, and accurate quantitative proportion. To achieve the process control objectives, this project needs to address the following issues:
(2) Configure and configure the control hardware for each section;
(3) Use an open communication network to connect each section into a distributed automation system.
The water extraction process of sugarcane plants exhibits multivariable, nonlinear, and time-varying characteristics, and the use of traditional feedback control methods cannot meet the control objectives. Therefore, it is necessary to study the combination of traditional PID, cascade control, and fuzzy control to achieve precise control of the production process; The ratio of Sugar cane juice is labor-intensive, and the ratio can not be adjusted at any time according to the change of material concentration to ensure the accuracy. Study the ratio control method of Sugar cane juice, build an accurate ratio model, and achieve quantitative and accurate ratio.
The cascade PID control mode is used to realize the automatic adjustment function of Sugar cane juice multi-stage heating and sterilization steam.
The pressure and temperature of the tubular multi-stage heating sterilization steam source are unstable, and are affected by the juice flow rate and initial temperature, requiring frequent adjustment. Manual adjustment is difficult to obtain stable temperature and pressure values, which affects the heating temperature and subsequent production. If single loop control is used, the disturbance of raw material and steam flow leads to untimely control effect, large deviation, poor control quality, and often cannot meet production requirements.
This article adopts a cascade control of the outlet temperature of the heater and the steam flow rate. In the heating control process, two PID controllers are connected in series to form a dual closed-loop control system. The output of the temperature controller is used as the set value of the flow controller, and the flow controller outputs to control the control valve of the steam heating pipeline.
After analyzing the section and considering the overall process, the control objects for primary heating designed in this project correspond to the following:
Temperature controller: PID module for heater outlet temperature;
Flow controller: Steam pressure PID module;
Control valve: 0.2Mpa steam inlet pneumatic control valve;
Flow detection transmitter: steam vortex street intelligent flow meter;
Temperature detection transmitter: an intelligent transmitter for primary heating outlet temperature.
By establishing a cascade PID program, good control effects were achieved in the temperature control of materials in both the primary and secondary heating sections of this project.
For the pretreatment Sugar cane juice conveying section, as the work area involves two workshops of the sugar factory (the pressing workshop and the sugarcane water production workshop), the conveying pipeline is several hundred meters long, and it is not easy to obtain the Dynamic equilibrium of flow, liquid level and pretreatment filtration effect by directly using the traditional PID control.
This article adopts a control method that combines manual rules and PID adjustment. Firstly, a set of preprocessing control rules is developed based on equipment operation flow and employee operation experience, and then judgment conditions are set. Based on the definition of the judgment conditions, which stage of control method is used is determined. When the production line is just starting to operate and there are significant changes in working conditions, due to the large fluctuations in material flow, the liquid levels of the tanks passing through will be subject to continuous fluctuations. In order to avoid the oscillation or delay caused by the direct introduction of PID control, the system will use empirical control algorithms to significantly increase or decrease the frequency of the frequency converter and the opening of related valves, Quickly approaching the set target at the liquid level of the material at all levels of the tank; When the liquid level of all levels of tanks approaches the target and the working condition is relatively stable, the second level judgment condition of the system is met. The traditional PID module is put into use to carry out fine control of the liquid level, so as to meet the requirement that the liquid level does not overflow during the production process, the pressure and flow are dynamically correlated and remain stable, which can maintain a good control effect, achieve dynamic balanced transmission of Sugar cane juice, and achieve accurate control of the liquid level, flow and pre-treatment effect, The ultimate goal is to achieve continuous and stable production.
The design goal of this article is for the controller to communicate with on-site intelligent devices through fieldbus, and multiple controllers are connected through Ethernet to form a digital, bidirectional transmission, and multi branch communication network, making the entire system open, integrated, and highly decentralized. According to the budget and process control requirements, it is determined to use multiple discrete controllers to take charge of the corresponding section control. Each section adopts a primary instrument on the site, and all instruments use intelligent transmitters for signal acquisition. The process parameters such as temperature, pressure, liquid level, flow, etc. are uniformly converted into readable data in intelligent transmitters. The data is read by the controller of each section, and then transmitted by Industrial Ethernet.
According to the process segmentation, control points, and control requirements of the entire production line, overall planning is carried out, while considering the targeted configuration of the system's openness and scalability under limited budget. The project adopts one set of S7-300 series PLCs and four sets of Smart 200 series PLCs as the subsystem control core for each section control. The membrane filtration section has the highest requirements, using the CPU315 DP-2 of the S7-300 series as the main station, 24 ET200M input and output modules through 3 IM153-1 link modules, and using the PROFI-BUS DP protocol to form the hardware system of the membrane section. The S7-300 can be competent for controlling membrane equipment sections with dense valves and numerous sensors. The raw material extraction, primary heating, pre physical filtration, secondary heating, and sugarcane plant water blending sections are divided into four systems, with each subsystem equipped with a set of control hardware centered on S7-200 Smart.
According to the characteristics of the control core, the entire system adopts two bus protocols: the membrane section adopts a PROFIBUS DP bus network, and the primary instrument is connected to ET200M through an isolator. ET200M and IM153-1 complete data interaction with the CPU; The remaining four S7-200 Smart controllers are connected to the primary instrument by configuring smart transmitters with Modbus protocol. The use of Modbus intelligent transmitters can solve the problem of 200 Smart controllers not being able to perform excessive analog input, while achieving the configuration goal of low end controllers to read instrument information through the field bus network.
The entire production system has three PCs as central control upper computers, which operate in fixed central control positions; Four touch screens serve as on-site human-machine operation interfaces for each process section. As an important section of the membrane equipment, a separate central control PC is assigned, and the SI-MATIC Win CC configuration software is configured to directly communicate with the S7 300 PLC. The other two central control upper computers, which can connect the entire factory for monitoring, use force control configuration software to solve the global monitoring function of different series of controllers at a lower cost. The touch screen directly uses the standard Win CC flexible for interface configuration. Each device in the workshop is configured with different IP addresses of the same network segment along with the corresponding control unit, and the data is ultimately shared with the force control configuration interface in the central control configuration. At the force control end, data interaction, data recording and reporting, alarm and other functions are achieved.
In this paper, MOXA Industrial Ethernet switch and photoelectric converter are configured to use optical fiber for long distance and 8-core network cable for short distance on site. All upper computers and control cores are integrated into the same LAN through Ethernet interface. PC upper computer, engineer station, PLC and touch screen can access each other, and the system has good scalability. By adopting the TCP/IP protocol, the entire production line and each section can be included in the main control system without the need for additional hardware equipment. The WEB publishing function of the force control software can be used to achieve remote control through the Internet, achieving data sharing between the management network and the control network. The energy consumption, material direction, and final product output of the entire production system can be well managed and controlled.
After the on-site bus automatic control system of the sugarcane plant water extraction process was put into operation, the production capacity of the entire line was increased, reaching a daily output of 40 tons, improving product quality, improving production efficiency, and reducing production costs; Improve product quality stability and avoid production accidents caused by human operation errors; Using the on-site bus automatic control system for sugarcane plant water extraction process, the entire production line can operate normally with only 8 operators, achieving the goal of high efficiency and labor saving.