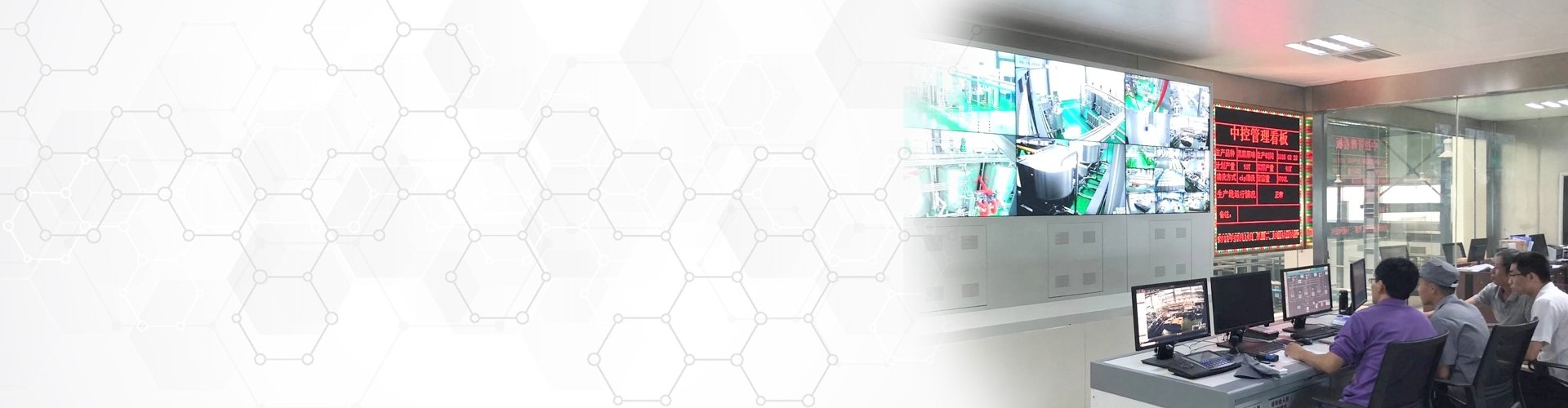
Spray Drying Tower is a device used to transform liquid substances into powder. It sprays liquid materials into hot air in the form of fine particles through spray to dry them quickly in a few seconds, so as to obtain the required powder products.
The working principle of spray drying tower is based on spray drying technology. This technology expands the surface area of materials by spray liquid into very fine particles, thus accelerating the evaporation speed and drying process. Specifically, the spray drying tower mainly includes the following steps:
1. Raw material preparation: prepare liquid materials to be dried into materials suitable for spray through pretreatment equipment (such as mixer and agitator), and generally adjust viscosity, solubility, concentration and other characteristics.
2. spray operation: spray the liquid materials into the spray drying tower with fine granular spray through the high-pressure nozzle or rotary atomizer. Hot air is injected into the spray at the same time to make liquid materials contact with hot air immediately.
3. Drying process: when spray particles enter the hot air and are exposed to the high temperature environment instantly, their water evaporates into steam instantly, making the particles gradually reduce. The remaining solid substances quickly condense into powder and enter the bottom of the drying chamber with the flow of hot air.
4. Collection and separation: Gas containing powder particles is introduced into the separator from the bottom of the drying chamber, and solid particles are removed through a bag filter or centrifugal separator, while recovering as much solid powder as possible.
Through this process, the spray drying tower can quickly dry the liquid materials into fine powder, which has the following advantages: high efficiency, complete the drying process in a short time; Controllability, adjust processing parameters as needed; Widely applicable, it can be used for material conversion in fields such as food, medicine, cosmetics, pesticides, etc.
In a word, spray drying tower is a common industrial equipment. Through spray drying technology, liquid materials can be rapidly transformed into powder, which is widely used in drying and crushing processes in various fields.
Features: upper inlet air, upper exhaust air, wide tower body, primary coalescence of droplets and secondary coalescence of fine powder, and three-stage drying spray drying system with built-in fluidized bed and vibrating fluidized bed, high and low temperature auxiliary drying and cooling functions. It is also called low temperature drying tower in the international industry.
Equipment characteristics of upper exhaust drying tower:
The equipment is flexible, professionally designed and suitable for different products;
Gas distributor, fully controlling the flow and speed of air flow;
Pressure nozzle, fully controlling the direction of atomization flow;
Multiple spray guns for one-time polymerization, fine powder for two-time polymerization and granulation of mobile products;
Control the particle size and structure of the product particles to make the product more soluble.
Basic working principle: the hot air quickly intersects with the spray droplets under the protection of the annular wind curtain through the diversion hot air distributor, so that the droplets vaporize in 0.4 seconds. The pressure of the hot air makes the dried powder quickly blown into the built-in fluidized bed at the bottom. The low heat air blown into the built-in fluidized bed carries out the second auxiliary drying of the product, and then the product enters the three-stage vibrating fluidized bed for the third low-temperature auxiliary drying, And cool to the packaging temperature for temporary packaging. The fine powder recovered by the powder catcher can also be secondary agglomerated and granulated through the built-in fluidized bed at the top or bottom of the tower, so as to improve the instant solubility of the product.
The upper exhaust pressure spray drying tower can be widely applied to the spray drying of powdered products made from solutions, suspensions and other liquids containing dry matter, and can be used in many fields such as food, additives, biology, medicine, chemical industry and so on.
Perfect spray drying tower design
Dust free, dry, safe and explosion-proof products cover a wide range
No product accumulation at the bottom of drying tower
Long production time reduces CIP cleaning times
Low energy consumption for low temperature gas discharge
Trouble free operation reduces downtime and saves energy
Excellent final powder quality
Optimal drying tower spray flow particle polyhedron geometry
Polymerized particles are porous and more soluble
Three stage drying with built-in fluidized bed and external fluidized bed in drying tower
Low temperature assisted drying reduces heat damage to products
Dehumidification and cooling of final products can be closely packed
Flow of gases and products
Atomizer
Center pipe fine powder injection pipe
Three nozzles around the central pipe
Peripheral series nozzle overlapping spray granulation
High efficiency granulation
Three nozzle fine powder granulation
Other nozzles overlap spray granulation
Low temperature zone of high-speed gas flow and built-in fluidized bed
Low density granulation
No fine powder circulation required
Spray granulation without nozzle overlap
Low temperature zone coalescence of low-speed gas flow and built-in fluidized bed
Product application:
Complete equipment production lines for powdered milk powder, infant formula powder, soybean milk powder, enzymolysis grain powder, plant fat powder, coconut powder, fruit and vegetable powder, separated protein powder, special medical food, solid beverage, food chemical industry, food additives, biopharmaceutical, etc.
Customized process of spray drying tower
Customizing a spray drying tower is a complex process involving multiple steps and technical considerations. The following is the detailed customization process:
1. Requirement analysis
• Communicate with customers: Gain a detailed understanding of their production needs, product characteristics (such as viscosity, concentration, particle size requirements, etc.), production capacity (hourly processing capacity), and quality standards for the final product.
• Determine the application scenario: know which industry the spray drying tower will be used in (such as dairy products, food, pharmaceuticals, etc.), so as to select the appropriate configuration.
2. Preliminary design
• Process design: Determine specific parameters of the drying process based on customer needs, such as feed temperature, outlet temperature, drying time, etc.
Equipment selection: Choose the appropriate nozzle type (rotary or pressure), heating method (electric heating or burner), separation device (cyclone separator or bag filter), etc.
Layout planning: Plan the overall layout of the drying tower, including the positions and connection methods of various parts such as the feeding system, drying chamber, and exhaust gas treatment system.
3. Detailed design
Structural design: Design the structure of the drying tower to ensure its strength and stability, while considering the convenience of maintenance and cleaning.
Material selection: Choose corrosion-resistant and easy to clean materials such as stainless steel, aluminum alloy, etc. based on the characteristics of the production materials and the usage environment.
Control system design: Design an automated control system that includes monitoring and adjusting key parameters such as temperature, pressure, and flow rate to ensure easy and efficient operation.
4. Manufacturing and assembly
• Component manufacturing: According to the design plan, manufacture various components of the drying tower to ensure dimensional accuracy and surface smoothness meet the requirements.
Assembly and debugging: Complete the assembly of the drying tower in the factory and conduct preliminary debugging to ensure that all components operate normally and all indicators meet the design requirements.
5. On site installation and debugging
Transportation and installation: Transport the drying tower to the customer's site and install it according to the design drawings to ensure that the equipment foundation is firm and the pipeline connections are correct.
On site debugging: Conduct final debugging on site, adjust various parameters, ensure the stable operation of the drying tower under actual production conditions, and meet product quality requirements.
Performance testing: Conduct performance testing on the drying tower, record various data, evaluate its drying effect and production capacity, and make optimization adjustments if necessary.
6. Training and Delivery
• Operation training: Provide customers with operation and maintenance training to ensure that they can proficiently use the drying tower and master daily maintenance methods.
• Document delivery: Provide complete technical documents such as equipment manuals, operation manuals, maintenance guides, etc., to facilitate customers' subsequent use and management.
After sales service: Establish an after-sales service system, provide regular inspections, troubleshooting, and technical support services to ensure the long-term stable operation of equipment.
7. Continuous improvement
• Feedback collection: Regularly collect customer feedback to understand issues and improvement suggestions during device use.
• Technical upgrading: according to customer feedback and technical development, continuously improve and optimize the design and performance of spray drying tower to improve product quality and user experience.