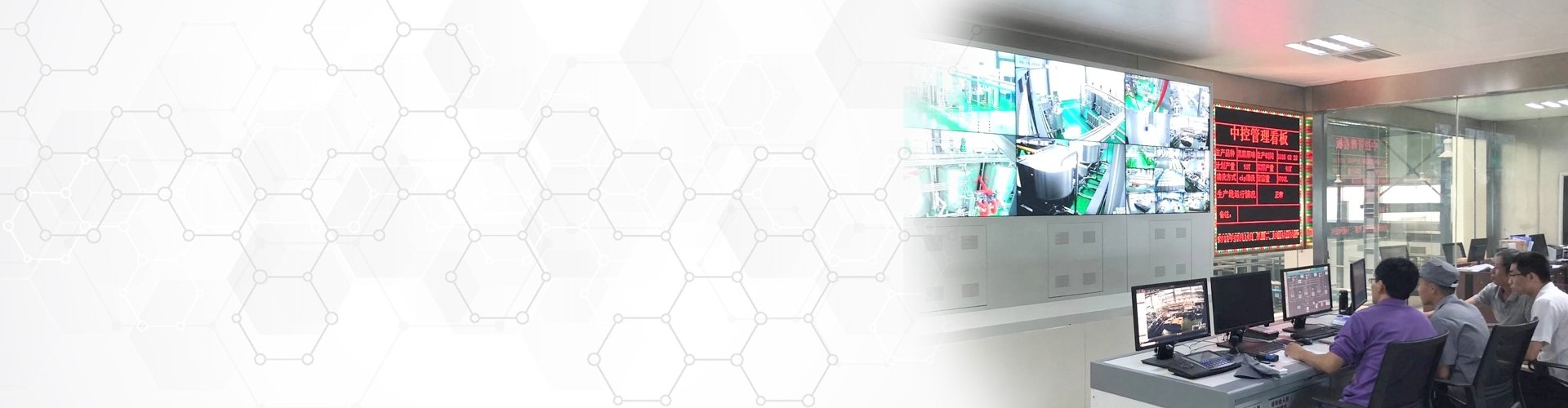
processing capacity: 20L/H.50L/H.100L/H.
Beverage formula, process, and flavor testing: ingredients, sterilization, homog-enization process test, aseptic filling at room temperature, product shelf life forhigh temperature filling product, taste test, etc. According to research and devel-opment requirements to determine the order of ingredients, temperature, stirringemulsification time, flavor test after proportioning ingredients. Determinehomogenization temperature, pressure, sterilization temperature, time, fillingtemperature and subsequent processing mode etc.; Clean the dosing tank andproduct discharge pipe before use; Necessary cleaning and disinfection arecarried on sterilization machine and filling machine; control the dosing processand temperature of the ingredients; necessary records and monitors on productsterilization and filling;
Testing machine for non-probiotic drinks fermented from yogurt, fruit and vegetable juices: mix thefermented raw materials and other auxiliary materials for batching - wash and clean sterile sterilizer andfilling room before use - sterilization and filling.
Featured Highlights
The Fully Automated PILOT Production Line has various features and highlights that make it stand out in modern production. Here are its main features and highlights:
1. Highly automated
Fully automated operation: The entire process from raw material input to finished product output is automated, reducing manual intervention and improving production efficiency.
Intelligent control system: Advanced PLC (programmable logic controller) and SCADA (data acquisition and monitoring control system) are used to achieve intelligent monitoring and management of the production process.
2. Flexibility and Scalability
Modular design: The production line consists of multiple modules, which can be flexibly configured and adjusted according to the production process of different products.
• Strong scalability: It is easy to add new functional modules or expand production capacity to meet the needs of enterprise development.
3. Efficient and energy-saving
Energy saving design: adopting high-efficiency motors and drive systems to reduce energy consumption and operational costs.
Optimize process: By optimizing the production process flow, reduce material waste and improve resource utilization.
4. High quality standards
• Precise control: Using high-precision sensors and control systems to ensure consistency and stability in product quality.
Strict testing: equipped with online testing and quality control systems, real-time monitoring of the production process to ensure the pass rate of each batch of products.
5. Safe and reliable
Multiple security protections: equipped with various security measures, such as emergency stop buttons, safety light curtains, etc., to ensure the safety of operators.
Stable operation: Using high-quality components and strict manufacturing processes to ensure long-term stable operation of the production line.
6. Remote monitoring and maintenance
• Remote monitoring: realize remote monitoring and management of production lines through Internet connection, and facilitate real-time data analysis and decision-making of enterprises.
• Remote maintenance: Provide remote fault diagnosis and maintenance services, quickly respond and solve problems in production.
7. User friendly
• Easy to operate: The human-machine interface is friendly, the operation is simple and intuitive, and easy to get started.
Training support: Provide comprehensive operation and maintenance training to ensure that customer employees can proficiently use the production line.
8. Environmental Design
Low emissions: Using environmentally friendly materials and technologies to reduce pollution emissions during the production process.
• Recycling: There is a waste recycling and reuse system in place to reduce resource waste.
9. Integrated solutions
One stop service: providing comprehensive service support from design, manufacturing, installation to commissioning.
• Customized services: Provide personalized customized solutions based on the specific needs of customers.
10. Complies with international standards
• Complete certification: Complies with ISO 9001 quality management system standards and has passed international certifications such as CE to ensure product quality and safety.
Determination process of fully automated pilot production line
The process of customizing a fully automated pilot production line typically involves the following steps to ensure that every step from requirement analysis to final delivery meets customer requirements. The following is the detailed customization process:
1. Requirement analysis
• Preliminary communication: Conduct preliminary communication with customers to understand their specific needs and expectations.
• Requirement research: Through questionnaire surveys, on-site inspections, and other methods, gain a deep understanding of the customer's production environment, product characteristics, and process requirements.
2. Scheme design
Preliminary plan: Based on the results of demand analysis, design a preliminary production line plan, including equipment selection, layout design, control system, etc.
Technical exchange: Conduct technical exchanges with clients to confirm the feasibility of the plan and make necessary adjustments.
3. Quotation and Contract Signing
• Detailed quotation: Provide a detailed equipment list, prices, and delivery time.
Contract signing: After both parties confirm that there are no errors, a formal contract will be signed.
4. Design and Manufacturing
• Detailed design: Conduct detailed design work according to contract requirements, including mechanical design, electrical design, control system design, etc.
Production and manufacturing: produce and assemble equipment according to design drawings and process requirements.
5. Installation and commissioning
Equipment transportation: safely transport production equipment to the customer's site.
Installation and debugging: Install and debug the equipment on site to ensure the normal operation of all parts.
Performance testing: Conduct comprehensive performance testing on the production line to ensure that the expected results are achieved.
6. Training and Acceptance
• Operation training: Provide equipment operation and maintenance training to customers' operators.
Acceptance and delivery: The customer conducts a final acceptance of the production line, confirms its accuracy, and officially delivers it for use.
7. After sales service
• Technical support: Provide continuous technical support and consulting services.
• Regular maintenance: Regularly maintain the production line to ensure long-term stable operation.
Matters needing attention
Communication: Maintain frequent communication with customers throughout the entire customization process and promptly resolve any issues that arise.
Quality control: Strictly control the quality of each link to ensure the reliability of the final product.
Flexible adjustment: Based on customer feedback and actual situation, adjust the plan flexibly to ensure that customer needs are met.
Through the above process, Shanghai Beyond Machinery can provide customers with high-quality and efficient fully automated pilot production lines, helping them achieve production automation and intelligence.