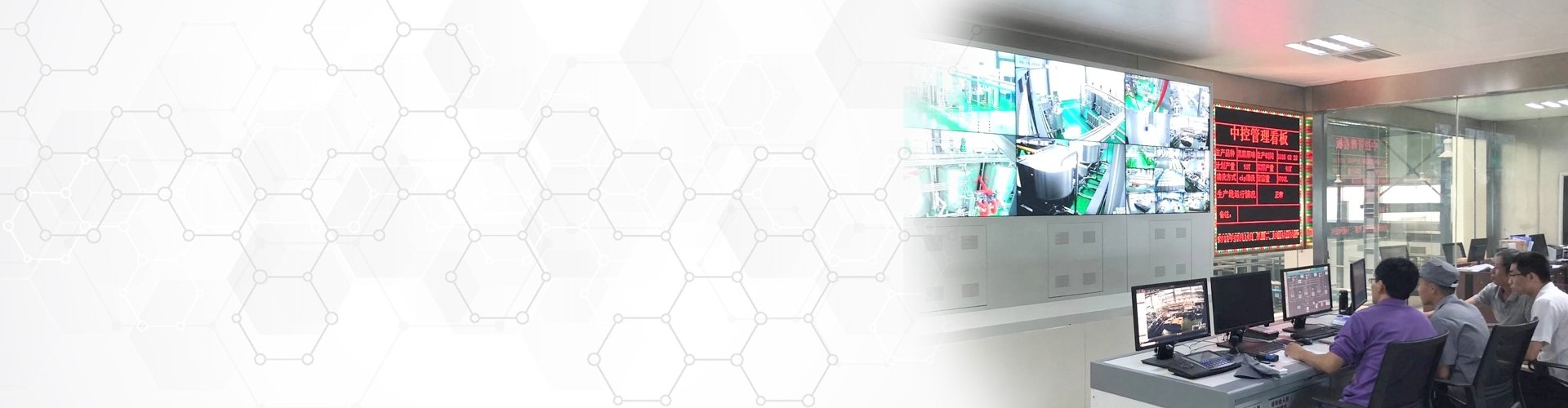
A shearing emulsification tank is a type of equipment used in the process of emulsification, which is the mixing of two immiscible liquids to form an emulsion. This tank is specifically designed to provide intense mechanical shearing action to break down the larger droplets of one liquid into smaller, more uniform droplets dispersed in the other liquid.
The tank usually consists of a cylindrical vessel with a motor-driven agitator or rotor-stator system. The agitator or rotor-stator generates high shear forces by rapidly rotating or vibrating, respectively. This intense shearing action applied to the two liquids promotes the formation of small droplets and enhances the stability and homogeneity of the resulting emulsion.
Shearing emulsification tanks are commonly used in various industries, including food and beverage, pharmaceuticals, cosmetics, and chemical manufacturing. They are utilized for producing emulsions such as oil-in-water or water-in-oil, where one liquid is dispersed as droplets within the continuous phase of the other liquid.
By controlling the operating parameters like rotational speed, residence time, and shear intensity, manufacturers can achieve desired emulsion characteristics such as droplet size distribution, stability, and viscosity. These tanks are essential in processes such as the production of creams, lotions, sauces, dressings, and various other emulsified products.
Overall, shearing emulsification tanks play a crucial role in the efficient and effective production of stable and homogeneous emulsions in various industrial applications.
Working process
1. Raw material preparation: Prepare two or more liquids (such as oil phase and water phase) that need to be emulsified, and add an appropriate amount of emulsifier according to the formula.
2. Feed: Send these liquids separately into the emulsification tank.
3. Start emulsification: Open the emulsification tank and rotate the rotor at high speed to generate shear force and stirring force.
4. Emulsification process: Under strong mechanical action, large droplets in the liquid are continuously broken into small droplets and stabilized by the action of emulsifiers.
5. Homogenization: continue mixing until the lotion reaches the required uniformity and stability.
6. Discharge: After emulsification is completed, the finished product is discharged from the emulsification tank for subsequent processing or packaging.
Application area
Food industry: producing milk, cream, mayonnaise, etc.
• Cosmetics industry: preparation of lotion, face cream, shampoo, etc.
Pharmaceutical industry: manufacturing various ointments and oral liquid formulations.
Chemical industry: producing paints, coatings, adhesives, etc.
Structure:
This tank has its own agitator with the sealing pairing of rotor and stator to ensure that the materials can be cut in high speed of near one million per minute. And anyone can be chosen among three stators in this structure.
It can be made to be single layer, double layer or three layer.
Technical Parameter:
Model |
Volume (L) |
Inner diameter (mm) |
Total height (mm) |
Shearer Motor power (KW) |
Mixer speed (r/m) |
RHTY-600 |
600 |
800 |
2140 |
7.5 |
2900/1450 |
RHTY-1000 |
1000 |
1050 |
2380 |
11 |
2900/1450 |
RHTY-1500 |
1500 |
1180 |
2450 |
15 |
2900/1450 |
RHTY-2000 |
2000 |
1340 |
2760 |
18.5 |
2900/1450 |
RHTY-3000 |
3000 |
1540 |
2870 |
22 |
2900/1450 |
Description of high speed mixing tank:
Made of sus304 stainless steel used for mixing sugar,mixing milk powder,emulsifier etc. agitator 2900rpm
this mixing tank is one of the most advanced mixing machines in China presently,
This tank has high speed agitator with the sealing pair of rotor and stator.
The customized process for a Multi Coupled Experimental Fermentation System typically includes the following steps:
1. Requirement communication: Firstly, we will have detailed communication with you to understand your specific requirements. This includes but is not limited to the required number of fermentation tanks, capacity size, desired control accuracy, and special functional requirements.
2. Scheme design: Based on the collected requirement information, our technical team will tailor a design scheme for you. This stage may involve the selection of equipment configuration, the design of process flow, and we will present you with a preliminary design plan to obtain feedback.
3. Confirm order: Once both parties have reached an agreement on the design proposal, the formal ordering process can begin. At this point, we will provide a clear price list and contract for your review and signature.
4. Manufacturing: After signing the contract, we will begin the production and assembly of the equipment according to the established specifications. This process may take some time, please be patient.
5. Quality inspection: After all components are assembled, a comprehensive quality inspection will be conducted to ensure that each machine meets the factory standards.
6. Shipping and installation: Products that have passed quality inspection will be properly packaged and arranged for transportation to the designated location. After arriving at the destination, professional personnel will be responsible for on-site installation and debugging until the equipment can operate normally.
7. Training guidance: In order to help customers better master the usage methods, we will also provide necessary operational training and technical support services.
8. After sales service: Finally, we promise to provide free maintenance services and other forms of technical support within a certain period of time to safeguard the interests of our customers.