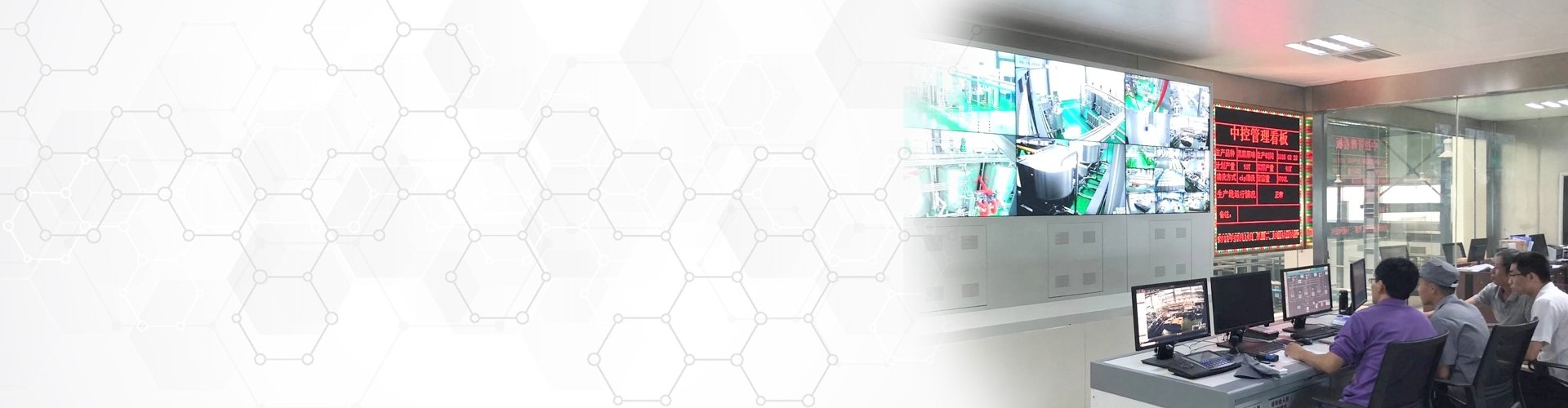
A wet pet food production line is a manufacturing system designed to produce wet or canned pet food products. It typically consists of several components and stages that work together to process and package the food.
Ingredient Preparation: Raw materials, such as meat, vegetables, grains, and supplements, are received and undergo various preparation processes. This may include sorting, cleaning, cutting, grinding, and mixing to create the desired product.
Mixing and Cooking: The prepared ingredients are mixed together in specific proportions to create a homogenous mixture. This mixture is then cooked under controlled conditions to ensure food safety and proper texture development.
Forming and Shaping: After cooking, the mixture is shaped into the desired form, such as chunks or patties, using specialized forming equipment. The size and shape can be adjusted according to the specific requirements of the pet food product.
Filling and Sealing: The formed pet food is then filled into cans or containers. This process is typically automated and involves precise filling to ensure consistent product weight and portion control. The containers are sealed to maintain product freshness and prevent contamination.
Sterilization and Cooling: The filled and sealed containers go through a sterilization process, which includes heat treatment to eliminate bacteria and extend shelf life. After sterilization, the containers are cooled down before proceeding to the next stage.
Labeling and Packaging: The cooled and sterilized pet food containers are labeled with product information, branding, and nutritional details. They are then packaged into boxes or cartons for transportation and storage.
Quality Control: Throughout the production line, quality control measures are implemented to ensure the pet food meets safety and quality standards. This includes regular sampling, testing, and inspection of raw materials, intermediate products, and final products.
It's important to note that specific equipment and machinery used in a wet pet food production line can vary depending on the scale of production and the desired product characteristics. Manufacturers may also incorporate additional steps or technologies to meet specific market demands or regulatory requirements.
• Pet wet grian process
Raw material delivery→Crushed raw materials→Preheating processing→ Blending emulsification→ Filling →Sterilization and ripening→Back packaging
In the design and production process of pet food production line, Beyond Company draws heavily on the technology and concept of food production line, which greatly improves the standard of pet food. And take the lead in introducing foreign advanced scraper heat exchanger technology to solve the problem that conventional heat exchangers can not exchange heat with high meat materials. And the food and pharmaceutical grade CIP cleaning and disinfection system is applied to the industry, which reaches a higher level of hygiene for pet food.
• Pet attractant process
Raw material delivery→Crushed raw materials→Preheat enzymatic hydrolysis→ Online sterilization→ Blending ingredients →Filling and spraying
Equipment Introduction
With the improvement of living standards, pets are increasingly entering people's lives, becoming a new fashion.
In the design and production process of pet food production lines, Beyond Company extensively draws on the technology and concepts of food production lines, greatly improving the standards of pet food. And took the lead in introducing and absorbing advanced scraper heat exchanger technology from abroad, solving the problem of conventional heat exchangers being unable to heat high meat materials. And apply the food pharmaceutical grade CIP cleaning and disinfection system to the industry, so that pet food can reach a higher level of hygiene.
Raw material grinding unit
The Beyond raw material grinding unit mainly consists of a frozen meat grinder, bone paste grinder, buffer tank, screw pump, etc. Mainly suitable for the preparation of pet flavoring agents such as chicken liver and cow liver, as well as the addition of slurry for the production of fresh meat in pet staple foods.
The equipment adopts a crushing and mincing integrated machine, which can directly crush and mince frozen meat raw materials at -18 ℃, greatly reducing the transportation process from cutting or crushing to the mincing machine, effectively solving the problem of material leakage during transportation, and greatly improving the production environment of traditional outdated production lines. Adopting a water bath temperature control system and a specially designed discharge elbow for the meat grinder, it can ensure smooth discharge from meat clamping to bone paste grinding.
Fresh meat addition unit
The Beyond Fresh Meat Addition Unit mainly consists of a fresh meat temporary storage tank, a screw pump, an emulsification pump, and a scraper heat exchange system. Mainly suitable for the addition of fresh meat in pet staple food production, the equipped scraper type heat exchanger fully solves the problems of traditional uneven heating, protein denaturation and solidification, and is suitable for fresh meat addition equipment for high meat products.
This equipment adopts a scraper type heat exchanger, and online water bath heating can effectively solve the problems of traditional slow heating, prolonged heating of materials, and clumping, providing the possibility for adding high meat staple foods. The scraped wall fresh meat temporary storage tank is used, heated in a water bath, and the material is heated gently to avoid protein denaturation caused by local overheating. At the same time, it effectively avoids tank wall sticking and equipment cleaning problems.
The raw materials and products of the pet canned food production line, the following are some key points:
1. Raw materials
Main raw materials
•
Meat: Chicken, beef, lamb, fish, etc. are the main sources of protein for canned pets.
•
Vegetables: Carrots, peas, beets, etc., provide vitamins and fiber.
•
Grains: rice, corn, wheat, etc., provide carbohydrates and energy.
•
Fruits: Apples, blueberries, etc., enhance flavor and nutritional value.
•
Animal by-products: liver, heart, lungs, etc., provide additional nutritional components.
Auxiliary raw materials
•
Minerals: calcium, phosphorus, iron, zinc, etc., supplementing essential trace elements.
•
Vitamins: Vitamins A, D, E, K, etc., enhance immunity and health.
•
Antioxidants: Vitamin E, BHA, BHT, etc., extend the shelf life of products.
•
Seasoning: salt, sugar, vanilla extract, etc., to improve taste and flavor.
•
Preservatives: Potassium sorbate, sodium benzoate, etc., prevent bacterial growth.
2. Product
Product Types
•
Single canned meat: such as canned pure chicken, canned pure beef, etc.
•
Canned mixed meat: such as canned mixed chicken and fish.
•
Canned vegetables and meat: such as canned mixed chicken and carrots.
•
Functional canned food: such as low-fat canned food for elderly pets, high protein canned food for kittens, etc.
•
Special formula canned food: such as grain free canned food, hypoallergenic canned food, etc.
Enzymatic hydrolysis reaction unit
The Beyond enzymatic hydrolysis reaction system mainly consists of an enzymatic hydrolysis reaction tank, a rotor pump, a temperature control system, etc. Mainly suitable for the production and processing of pet flavoring agents.
This equipment adopts dual motor dual speed reverse wall scraping mixing and paddle mixing, which can fully mix high-quality meat pulp materials evenly, while effectively avoiding problems such as material wall scraping and uniform temperature distribution. The unique bottom tank bottom valve design forms a complete arc seal with the tank bottom seal head, effectively avoiding dead corners in the pipeline. The new weighing module design can accurately measure the addition of reaction base materials, auxiliary materials, moisture, etc., achieving data-driven operations.
Customizing a pet canned food production line involves multiple steps and detailed planning. Here is a detailed customization process to help you successfully complete the project:
1. Market research and demand analysis
•
Market research: Understand the demand for canned pet food in the target market, including variety, taste, packaging form, etc.
•
Competitive analysis: studying competitors' products and market strategies to identify differentiated advantages.
•
Customer demand: Collect feedback and suggestions from potential customers to determine the positioning and features of the product.
2. Project planning and feasibility study
•
Project objective: Clarify the overall goals of the project, including output, quality standards, market share, etc.
•
Feasibility study: Evaluate the feasibility and risks of a project, including technical feasibility, economic feasibility, legal compliance, etc.
•
Budget preparation: Develop a detailed project budget, including expenses for equipment procurement, factory construction, raw material procurement, etc.
3. Site selection and design of factory buildings
•
Site selection: Choose a location with convenient transportation, sufficient water sources, and clean environment.
•
Factory design: Reasonably plan the layout of the factory, including production areas, storage areas, office areas, etc.
•
Environmental protection facilities: Ensure that the factory meets environmental requirements and install necessary sewage treatment and exhaust gas treatment equipment.
4. Equipment selection and procurement
•
Production line equipment: Select equipment suitable for producing pet cans, such as raw material processing equipment, filling machines, sealing machines, sterilization pots, cooling systems, packaging machines, etc.
•
Auxiliary equipment: Choose necessary auxiliary equipment such as conveyor belts, elevators, cleaning machines, etc.
•
5. Production process and technology
•
Raw material processing: Pre treatment such as cleaning, cutting, and mixing of meat, vegetables, grains, and other raw materials.
•
Formula design: Based on the nutritional needs of pets, design scientifically reasonable formulas to ensure the nutritional value of the product.
•
Filling and sealing: Fill the prepared pet food into cans and seal them.
•
Sterilization and cooling: Perform high-temperature sterilization treatment on canned food and then cool it to room temperature.
•
Quality inspection: Conduct quality inspections on key links in the production process to ensure product safety and quality.
6. Packaging and labeling
•
Packaging design: Design beautiful and practical packaging to enhance the market competitiveness of the product.
•
Label identification: According to relevant regulations, correctly label the product name, ingredients, production date, shelf life, and other information.
•
Packaging materials: Choose appropriate packaging materials, such as aluminum cans, plastic cans, etc., to ensure the sealing and safety of the product.
7. Sales and Marketing Promotion
•
Sales channels: Establish diversified sales channels, such as pet stores, supermarkets, e-commerce platforms, etc.
•
Market promotion: Develop effective marketing plans, including advertising, promotional activities, social media marketing, etc.
•
Customer Service: Provide high-quality customer service and establish a good brand image.
8. Quality Management System
•
ISO certification: Apply for ISO 9001 quality management system certification to enhance the management level and product quality of the factory.
•
HACCP system: Establish a Hazard Analysis and Critical Control Point (HACCP) system to ensure food safety.
•
Employee training: Regularly train employees to improve their operational skills and quality awareness.
9. Regulations and Compliance
•
Legal regulations: Understand and comply with local pet food production laws and regulations to ensure legal and compliant production.
•
Licensing and Certification: Apply for necessary production licenses and product certifications, such as FDA certification, CE certification, etc.
10. Project Implementation and Management
•
Project management: Develop a detailed project implementation plan, clarify the goals and timeline for each stage.
•
Progress tracking: Regularly check the progress of the project and promptly resolve any issues that arise.
•
Risk management: Identify potential risks in the project and develop corresponding response measures.
11. Trial operation and debugging
•
Equipment debugging: Debugging production equipment to ensure its normal operation.
•
Trial production: Conduct small-scale trial production to inspect the quality and production process of the product.
•
Optimization and improvement: Based on the results of trial production, optimize and improve the production process and equipment.
12. Formal production and continuous improvement
•
Formally put into production: After completing all preparatory work, it is officially put into production.
•
Continuous improvement: Regularly evaluate the production process and product quality, continuously optimize and improve.
Conclusion
Customizing a pet canned food production line requires comprehensive consideration of market research, project planning, factory design, equipment selection, production technology, quality management, and market promotion.