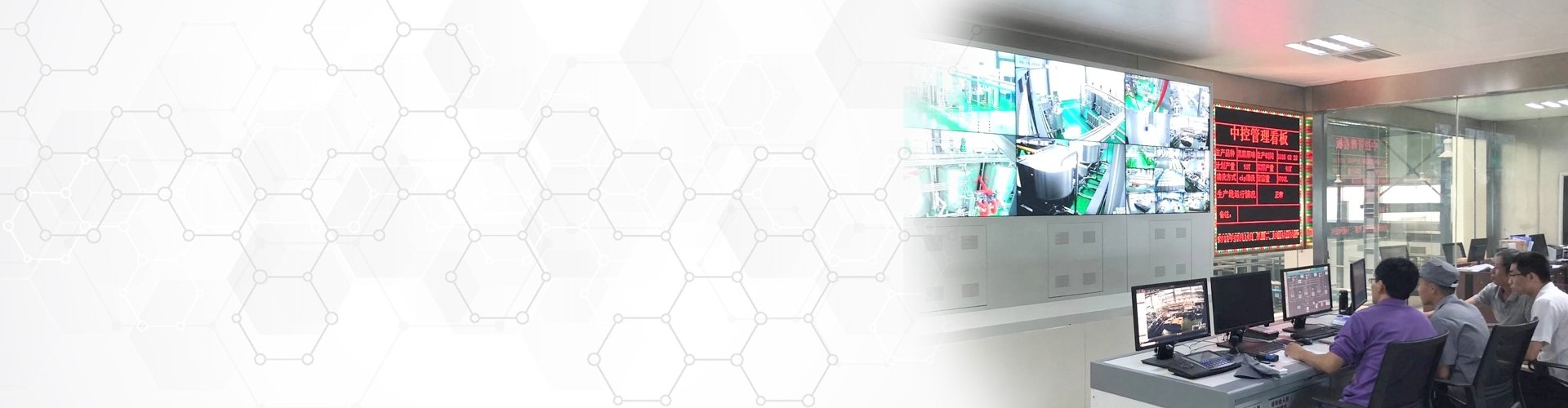
MVR evaporator is an application of thermal energy recovery technology, whose principle is to increase the steam production of the evaporator through mechanical compression. In traditional evaporation processes, water or other liquids are heated to evaporate, generating steam, which then further condenses into a liquid. The MVR evaporator uses a compressor to compress the condensed steam again into high-temperature and high-pressure steam, which is then injected into the evaporator again, achieving energy recycling.
The advantages of MVR evaporator include:
Energy saving: Due to the fact that steam does not require external heating but is recycled through efficient compressors, MVR evaporators have higher energy efficiency compared to traditional evaporators and can significantly reduce energy consumption.
Reduce environmental pollution: The MVR evaporator does not require additional fuel for heating during operation, reducing exhaust emissions and greenhouse gas emissions, making it more environmentally friendly.
Reduce operating costs: The MVR evaporator does not require external heating, which can reduce operating costs and reduce fuel procurement and waste gas treatment costs.
The application fields of MVR evaporators are very wide, mainly including the following aspects:
Salt water treatment: When used for seawater desalination or extracting useful substances from saline water, MVR evaporators can effectively achieve water evaporation and concentration, thereby obtaining pure water or concentrate.
Wastewater treatment: In industrial production processes, the dissolved substances in wastewater can be concentrated through MVR evaporators to meet discharge standards and recover valuable substances.
Food industry: In the food processing process, MVR evaporators can be used for food concentration, dehydration and other processes, such as juice concentration and dairy product concentration.
Chemical process: MVR evaporators are widely used in solvent recovery, concentration, and distillation processes in the chemical industry, playing an important role in improving product purity and reducing energy consumption.
In summary, MVR evaporator is an efficient, energy-saving, and environmentally friendly evaporation technology with broad application prospects in multiple fields.
Performance characteristics and scope of application:
1)No waste heat steam emissions, energy-saving effect is very significant, which is equivalent of 10 effect evaporator.
2 )Using this technology can achieve to countercurrent washing of secondary steam, therefore the dry matter content in condensed water is far lower than the number of evaporator.
3)Using low temperature negative pressure evaporation (50-90 ℃), help to prevent the degeneration resulted from high temperature evaporation.
4)MVR evaporator is a substitute of traditional multi-effect falling-film evaporator, is based on single effect evaporator through the reuse of the secondary steam countercurrent washing and recompression. All material that applicable for single effect and multi-effect evaporator, are suitable for use in the MVR evaporator, technically have the substitutability. It has perfect characteristics of environmental protection and energy saving. Because of its significant energy-saving effect, MVR evaporator technology started rapid development in foreign countries at the beginning of 70's, now is widely used, which is used in industrial wastewater treatment and dairy, sugar, starch, alumina, papermaking, caprolactam, seawater desalination, coking plant (recovery of sulfur dioxide production sulfur ammonia), salt chemical industry, and other many production areas.
Applicable range
Mechanical vapor compression MVR or MVC (Mechanical Vapor Compression) evaporator, the principle is to use the secondary steam which is produced through compressing the steam by the steam compressor , secondary steam heat and temperature is increased by the compressor, steam compressed into the evaporator as the heat source, again makes the raw material liquid start evaporation, so there is no need to rely on external fresh steam, just need to rely on the evaporator system itself circulating to achieve the purpose of evaporation. Through the PLC control system, configuration software and engineering software to control the temperature, pressure, speed motor system, maintain stable, intelligent and efficient operation of the evaporator.
Technical parameters (evaporation according to the customer need to design)
Model |
BYMVR-0.5 |
BYMVR-1 |
BYMVR-1.5 |
BYMVR-2 |
BYMVR-5 |
BYMVR-10 |
BYMVR-15 |
Evaporation capacity |
500kg/Hr |
1000kg/Hr |
1500kg/Hr |
2000kg/Hr |
5000kg/Hr |
10000kg/Hr |
15000kg/Hr |
Inlet saturated steam capacity (kg/Hr) |
500 |
1000 |
1500 |
2000 |
5000 |
10000 |
15000 |
Inlet saturation temperature (°C) |
55.295 |
71.631 |
82.109 |
90 |
90 |
90 |
90 |
Outlet temperature (°C) |
12.590 |
14.145 |
15.185 |
16.000 |
16.000 |
16.000 |
16.000 |
Outlet the saturation temperature (°C) |
67.885 |
85.776 |
97.294 |
106.000 |
106.000 |
106.000 |
106.000 |
Inlet saturation pressure kPa (A) |
15.975 |
33.441 |
51.567 |
70.117 |
70.117 |
70.117 |
70.117 |
Inlet saturation pressure kPa (A) |
28.432 |
59.596 |
91.921 |
125.029 |
125.029 |
125.029 |
125.029 |
Compression ratio |
1.780 |
1.782 |
1.783 |
1.783 |
1.783 |
1.783 |
1.783 |
Motor power (kw) |
40 |
55 |
75 |
95 |
132 |
550 |
640 |
|
0.795 |
0.7971 |
0.7985 |
0.7997 |
0.7997 |
0.7997 |
0.7997 |
Outlet volume flow (m³/s) |
22.736 |
22.795 |
22.837 |
22.87 |
22.87 |
22.87 |
22.87 |
|
4X4X10 |
6X4.5X12 |
8X5.5X14 |
8X5.5X14 |
9.5X6X15 |
12.6X6.5X17 |
13.6X7X17 |