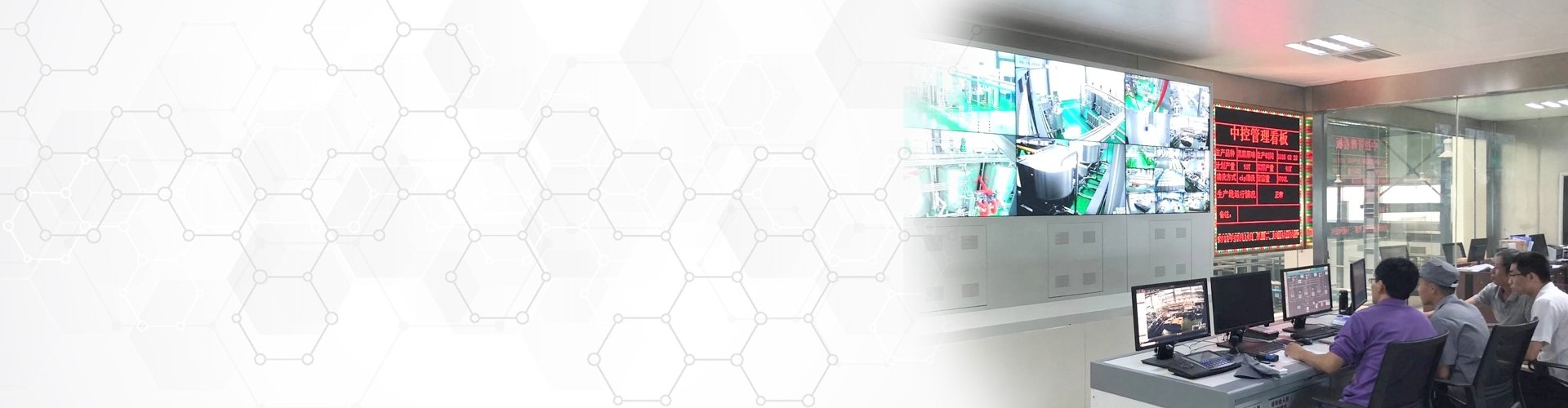
Fermentation tank, also known as fermentation vessel or bioreactor, is the core equipment used to cultivate microorganisms or cells and perform biochemical transformation during the fermentation process. It is widely used in the food industry (such as brewing beer, yogurt production), biopharmaceuticals, chemicals, and biofuels. The design of a fermentation tank aims to create a suitable environment where microorganisms can grow, reproduce, and undergo specific metabolic processes, thereby producing the required products such as alcohol, lactic acid, antibiotics, or biofuels.
The main components of a fermentation tank include:
1. Tank body: usually made of stainless steel material, ensuring a sterile internal environment and withstanding certain pressure and temperature changes.
2. Stirring system: By using a stirring paddle, the microorganisms and nutrients in the culture medium are fully mixed, increasing mass transfer efficiency and biological reaction rate.
3. Ventilation and exhaust system: providing sufficient oxygen for microorganisms and eliminating metabolic waste such as carbon dioxide.
4. Temperature control system: Maintain a constant temperature inside the tank to optimize the growth conditions of microorganisms.
5. Sensors and control systems: Monitor and control key parameters such as pH value, dissolved oxygen, temperature, etc. inside the tank to ensure that the fermentation process proceeds as expected.
6. Emissions and sampling ports: facilitate regular sampling inspections and the collection of final products. The fermentation process may involve aerobic fermentation (such as yeast fermentation) or anaerobic fermentation (such as the fermentation of certain lactic acid bacteria), so the configuration of the fermentation tank will be adjusted according to specific process requirements.
With the advancement of technology, modern fermentation tanks are increasingly tending towards automation and intelligence, which can achieve more precise control and higher production efficiency.
The key points of fermentation tank technology mainly focus on the following aspects to ensure efficient, safe, and controllable biological fermentation process:
1. Material and Design: Choose corrosion-resistant and easy to clean materials, such as 304 or 316L stainless steel, and a reasonable tank design to ensure sterile operation and easy maintenance. The tank body must be able to withstand certain internal pressure and temperature, and have good insulation performance.
2. Stirring and mixing technology: Adopting an efficient mixing system, such as a motor drive device with different shaped mixing paddles, to improve the uniformity of the medium and mass transfer efficiency. Variable frequency speed regulation can flexibly control the stirring speed to meet the fermentation needs of different stages.
3. Gas supply and management: Efficient ventilation systems, such as microporous aeration or jet ventilation, ensure sufficient oxygen supply to microorganisms. Simultaneously equipped with CO2 removal or recovery systems to maintain gas balance and reduce pollution risks.
4. Temperature and pH control: A high-precision temperature control system, such as an electric heating jacket or cooling coil, combined with an automatic regulating valve, ensures stable temperature inside the tank. Use pH electrodes and a system that automatically adds acid-base solutions to maintain an ideal pH environment.
5. Pressure control and safety: Equipped with pressure sensors and safety valves, it can maintain the required positive or negative pressure state for fermentation and quickly release pressure in case of abnormalities, ensuring safety.
6. Online monitoring and automation control: Integrate multiple sensors (such as dissolved oxygen CO2、 Temperature PH and automation control system are used to achieve real-time monitoring and automatic adjustment of the fermentation process, improving the accuracy and efficiency of process control.
7. Sterile operation and CIP/SIP: Adopting the concept of sterile design, ensuring sterile operation in feeding, sampling, discharge and other processes. Supports in situ cleaning (CIP, Clean in Place and in situ sterilization (SIP), Sterilization-in-Place), Simplify the operation process and improve production efficiency.
8. Flexibility and Scalability: Modular design allows fermentation tanks to be flexibly combined according to production needs, easy to expand or adjust, and meet production requirements of different scales.
9. Data management and analysis: Integrate information management systems to record and analyze fermentation process data, provide a basis for optimizing fermentation conditions and improving product quality, and achieve the management goals of smart factories. These technical points together form the foundation of modern fermentation technology, driving the development and innovation of the biological manufacturing industry.
The application of fermentation tanks covers multiple industries, and their core function is to provide a controllable environment for microbial growth and metabolism, thereby producing various useful metabolic products.
The following are some main application areas:
Food and beverage industry: • Brewing: the production of beer, wine, Baijiu and other alcoholic beverages, which produce alcohol by yeast fermentation of sugar. • Dairy products, such as yogurt and cheese, use lactic acid bacteria to ferment lactose to produce lactic acid, change the taste of the product, and extend its shelf life Bread and baking: The dough fermentation process also utilizes yeast fermentation to produce carbon dioxide, causing the dough to expand in volume Biopharmaceutical industry: • Antibiotic production: such as penicillin, erythromycin, etc., produced through specific microbial fermentation Vaccine manufacturing: Some vaccines involve microbial or cell culture, and fermentation tanks are one of the key equipment.
The production of biotechnology drugs, such as recombinant proteins such as insulin and growth hormone, requires strict aseptic environment and precise fermentation control Chemical and biofuel industries: • Bioethanol: As a type of renewable energy, it is produced through fermentation of corn, sugarcane, or cellulose biomass Biodiesel: produced through microbial fermentation and transformation of oily substances Organic acid production, such as citric acid, acetic acid, etc., is widely used in the food, pharmaceutical, and chemical industries.
Agriculture and Environmental Protection: • Biofertilizers: Using microorganisms to ferment organic waste to produce organic fertilizers and improve soil fertility Wastewater treatment: Industrial wastewater is treated through anaerobic or aerobic fermentation of specific microorganisms to remove harmful substances Health products and cosmetics industry: • Probiotic products, such as probiotic beverages and capsules, are produced through fermentation of specific bacterial strains Functional ingredients, such as hyaluronic acid and collagen, can be used in skincare and health products and extracted through microbial fermentation.
The application of fermentation tanks not only promotes technological innovation in traditional industries, but also provides strong technical support for emerging bioeconomy, and is an important bridge connecting biological research and industrial production.
Technical parameters
Model |
Diameter |
External diameter |
Height(mm) |
Insulation(δ) |
Jacket(δ) |
Diameter of inlet/outlet |
BYFG-500 |
φ500 |
800 |
2140 |
50 |
1.5 |
φ38/φ51 |
BYFG-1 |
φ1000 |
1050 |
2380 |
50 |
1.5 |
φ38/φ51 |
BYFG-1.5 |
φ1500 |
1180 |
2550 |
50 |
1.5 |
φ38/φ51 |
BYFG-2 |
φ2000 |
1340 |
2760 |
50 |
1.5 |
φ38/φ51 |
BYFG-2.5 |
φ2500 |
1420 |
2940 |
50 |
1.5 |
φ38/φ51 |
BYFG-3 |
φ3000 |
1540 |
3050 |
50 |
1.5 |
φ38/φ51 |
BYFG-4 |
φ4000 |
1650 |
3200 |
50 |
1.5 |
φ38/φ51 |
BYFG-5 |
φ5000 |
1780 |
3250 |
50 |
1.5 |
φ38/φ51 |
BYFG-6 |
φ6000 |
1900 |
3350 |
50 |
1.5 |
φ38/φ51 |
BYFG-8 |
φ8000 |
2100 |
3800 |
60 |
1.5 |
φ65/φ51 |
BYFG-10 |
φ10000 |
2300 |
4050 |
60 |
1.5 |
φ65/φ51 |
BYFG-12 |
φ12000 |
2520 |
4450 |
60 |
1.5 |
φ65/φ51 |
Installing and debugging fermentation tanks is a complex and highly specialized process that involves multiple technical aspects such as mechanical, electrical, and automatic control.
The following are the basic steps and precautions for installing and debugging a fermentation tank: Preparation before installation
1. On site evaluation: Confirm whether the ground bearing capacity, space size, water and electricity supply, ventilation conditions, etc. of the installation location meet the requirements.
2. Infrastructure: Design concrete foundations based on the weight and size of the tank, and ensure that they are fully cured before installation.
3. Technical data review: Carefully read the equipment manual, installation guide, and drawings to understand the equipment structure, installation requirements, and safety regulations.
Installation process
1. Lifting in place: Use professional lifting equipment to carefully lift the fermentation tank to the predetermined position, ensuring smooth placement.
2. Connecting pipes and accessories: including feed pipes, discharge pipes, exhaust pipes CIP pipeline SIP pipelines, sensor cables, etc., all connections must be well sealed to prevent leakage.
3. Electrical and self-control system installation: Install electrical components such as motors, controllers, sensors, etc., lay cables and control circuits to ensure circuit safety and reliability.
4. Installation of safety devices: Install pressure gauges, safety valves, emergency relief devices, etc. to ensure production safety.
Debugging stage
1. Water pressure test: Conduct a water pressure test on the tank and its connecting pipes to check for leaks and verify the sealing performance of the tank.
2. Empty running test: Start the mixing system, temperature control system, ventilation system, etc., conduct sterile water circulation test, and observe the working status of each system.
3. Calibration and calibration: For temperature sensors Calibrate pH sensors, dissolved oxygen sensors, etc. to ensure measurement accuracy.
4. Simulated fermentation test: Conduct a simulated fermentation test under sterile conditions, test the stability and control accuracy of the entire system, and adjust and optimize various parameters.
5. Cleaning and disinfection: After completing the debugging, comprehensive CIP cleaning and SIP sterilization will be carried out, and preparations will be made for formal production.
Attention
Safety First: Throughout the installation and debugging process, it is necessary to strictly follow the safety operating procedures and wear necessary protective equipment Professional operation: The installation and debugging should be carried out by experienced technicians to avoid improper operation and damage to the equipment Recording and documentation: Detailed documentation of each step of operation and test results, providing a basis for subsequent maintenance and troubleshooting Environmental control: Ensure the cleanliness of the installation and debugging environment, especially in sterile environments, to avoid pollution risks. Proper installation and debugging of the fermentation tank is crucial to ensuring production efficiency and product quality, therefore every step needs to be executed meticulously.