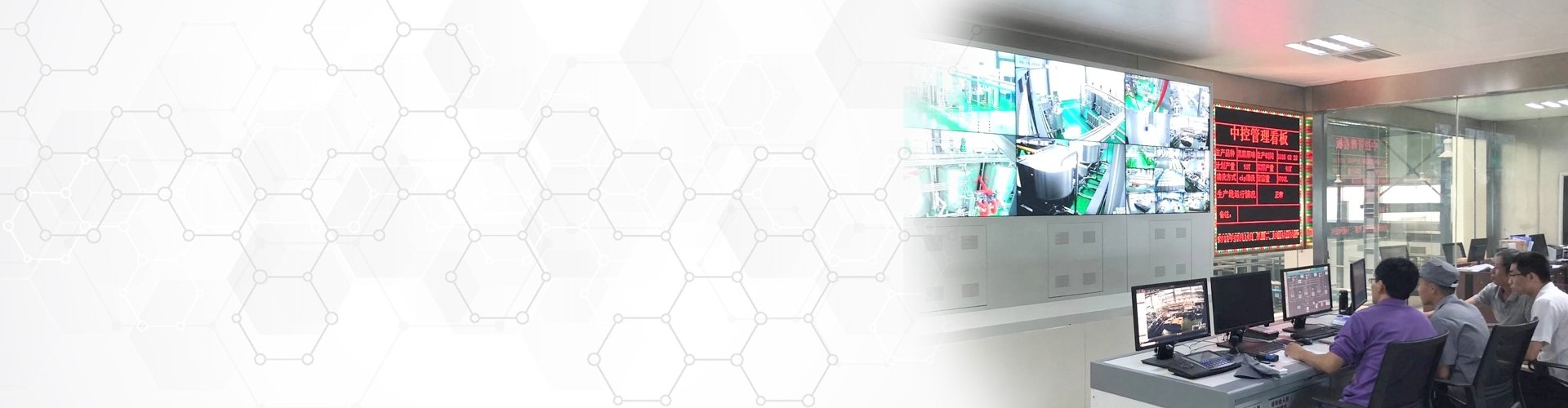
Description of apple processing line
The Apple and Pear Processing Line is a specialized production line designed to process apples and pears into various products such as juice, puree, sauce, and slices. It consists of several machines that perform different tasks in the processing of apples and pears.
Fruit Washing Machine: This machine is used to remove dirt, dust, and impurities from the fruits before further processing.
Fruit Sorting Machine: The sorting machine is equipped with sensors that detect the size, color, and quality of the fruits. It separates the fruits into different grades for further processing.
Fruit Peeling Machine: This machine removes the peel from the fruits using rotating brushes or blades. It ensures efficient and uniform peeling of the fruits.
Fruit Pitting Machine: This machine removes the cores and seeds from the fruits. It can be adjusted to accommodate different sizes and types of apples and pears.
Fruit Slicing Machine: This machine slices the apples and pears into uniform thickness. It can be adjusted to produce different slice sizes according to the requirements.
Fruit Grinding Machine: This machine grinds the fruits into a fine puree or pulp. It is commonly used in the production of fruit juice and sauce.
Fruit Pressing Machine: This machine extracts the juice from the fruit pulp. It applies pressure to the pulp, separating the juice from the solids.
Fruit Pasteurization Machine: The pasteurization machine heats the juice to a specific temperature to kill any bacteria or microorganisms, ensuring the safety and shelf life of the product.
Fruit Packaging Machine: This machine packages the final product, whether it's juice, puree, sauce, or slices, into containers or bottles. It can also seal and label the packages.
These machines can be customized according to the specific needs and capacities of the processing line. They are designed to optimize efficiency, improve productivity, and maintain the quality of the processed apple and pear products.
System Advantages
1) The processing capacity is varied from 60 tons/day to 1500 tons/day.
2) This line can handle similar fruits with similar characteristics.
3) Automatic disinfection liquid concentration control system, effectively guarantee the sterilization effect and control the disinfection residue.
4) Efficient crusher improved the high output percentage of apples and pears.
5) Using efficient belt juice extractor to improve the juice efficiency and the output percentage.
6) The production process fully automatic PLC control to reduce the labor intensity and Improve production efficiency.
7) Low-temperature vacuum evaporation 8 Greatly reduce the flavor substances and nutrient losses.
8) A variety of energy recovery measures , increased the energy utilization and greatly reduce production cost.
9) Tubular UHT sterilizer and Aseptic filling machine, Isolated from the pollution of bacteria,ensure the safety of the food and extend the shelf life of the product.
10) A complete set of production with self CIP system reduce the labor intensity and ensure the high level sanitation.
Raw materials and products of apple juice processing production line
1. Raw materials
The raw materials of apple juice processing production line mainly include fresh apples and other auxiliary materials. The following is a detailed description:
1. Fresh apples
• Variety selection: Choose apple varieties suitable for juicing, such as Fuji, Red Fuji, Granny Smith, Golden Delicious, etc. Different varieties of apples have different flavors and nutrients.
• Quality standards: Choose fresh apples with moderate maturity, no pests and diseases, and no rot. Apples should be kept intact as much as possible to avoid damage to reduce the risk of contamination.
2. Water
• Use: Used for washing apples and preparing apple juice.
• Water quality requirements: Must meet drinking water standards. It is recommended to use purified water sources to ensure safety and hygiene.
3. Food additives (optional)
• Vitamin C (ascorbic acid): used to prevent oxidation and maintain the color and taste of apple juice.
• Stabilizers: such as xanthan gum, pectin, etc., used to improve the texture and stability of apple juice and prevent precipitation.
• Sweeteners: such as sucrose or stevioside, adjust the sweetness according to market demand.
• Flavor: natural or synthetic flavor, used to enhance the aroma of apple juice.
2. Product
The main product of the apple juice processing line is finished apple juice, which can be divided into the following types according to different production processes and market demands:
1. Pure apple juice
• Features: no other ingredients are added, retaining the original flavor and nutrition of apples.
• Production process: cold pressing or hot pressing technology is used to ensure that the natural ingredients in apples are retained to the maximum extent.
• Applicable people: consumers who pay attention to health and pursue natural drinks.
2. Concentrated and reconstituted apple juice
• Features: made by concentration and reconstitution process, easy to transport and store.
• Production process: first concentrate the apple juice to a certain concentration (such as 65-70 Brix), and then add water to dilute and restore it to the original juice state.
• Applicable people: widely used in the beverage industry, as a raw material for further processing.
3. Modulated apple juice
• Features: add appropriate amount of water, sugar, vitamins and other ingredients on the basis of pure apple juice to adjust the taste and nutritional content.
• Production process: mixing tank preparation, filling after homogenization treatment.
• Applicable groups: meet the needs of consumers with different taste preferences.
4. Functional apple juice
• Features: add specific functional ingredients to apple juice, such as dietary fiber, probiotics, minerals, etc., to give it specific health benefits.
• Production process: additional functional ingredients need to be added and strict quality control is carried out.
• Applicable groups: consumers with special health needs, such as weight loss, gastrointestinal conditioning, etc.
Technical Data For apple processing line
Brand Name: | Shanghai Beyond |
Model Number: | BY-AL |
Capacity | 5-50T/H |
Raw material | Fresh apple/pear |
End product | NFC fresh apple/pear juice, concentrated apple/pear juice, clear apple/pear juice |
Juice yield | 60-75% |
Fresh fruit input brix | 10-12brix(for fresh fruit) |
End product output brix | 65-72Brix |
Package for end product | Aseptic large bag in drum/ glass bottle/PET bottle, Roof type carton box/ brick shape carton |
Certification: | ISO9001/CE/SGS |
Main material for machines | SUS304 or SUS316 |
Place of Origin: | China |
Manufacturer history | More than 10years |
Voltage | 380V 50Hz/110V 60hz/415V 50Hz |
Power consumption(Kw) | energy saving type, about 100-500kw, |
Operator needed | About 6-20persons |
Cooling water consumption | About 80-300M3 |
Steam consumption | About 300-5000T/H, |
Factory space needed | About 500-5000Sqm |
Warranty | 12 months after commissioning |
After sales service |
Engineers available to service machinery overseas |
Technological Flowchart Of Apple&Pear Processing line:
Concentrated and NFC apple/pear juice:Fresh apples or pears after washing and sorting,crushing,color-protecting,
belt press juice,enzyme treatment,ultra-filtration treatment,disk separator,then we will get the fresh clear apple
juice.If we concentrated apple juice,then we will obtain the concentrated apple juice,then after sterilizing,the end
products will be filled into aseptic bags;If we do not concentrate,then will get NFC clear apple juice,after sterilizing,
The end products will be filled into aseptic bags in bulk or blended with water or other additives,homogenizing and
degassing filled into small bottles.
Reconstituted apple/pear juice:Use concentrated apple juice as raw materials,after blending with water,sugar and
other additives homogenizing,vacuum degassing,sterilizing,then filled into small bottles or cartons.
Apple&Pear washing and sorting machine
Before cleaning,there are a lot of microorganisms on the surface of the apple.By air blowing washing,the microorganisms are reduced to 5%.
The cleaning effect depends on the cleaning temperature and time,PH value,hardness,and mineral content of the cleaning solution.
The fruit is sorted by roller conveyor so the apple is turned during the transporting process.The advantage is that it can more thoroughly remove bad and insect fruits and mechanical wounds fruits,weeks,and foreign matters.
Apple/Pear crushing machine
Fresh apple or pear after crushing,the piece size is 3-9mm even particle,The crushinng methods is using of mechanical crushing.The principle is crushing by roller squeezing and blade cutting.Finally,the sieve surface with a certain aperture is the size of the fruit particles in accordance with the standard.
Apple juice color protecting system
During the crushing or process of the apple,the apple pulp is in contact with the air,which easily causes the pulp to undergo oxidative browing.The mixed solution of ascorbic acid and citric acid can be used for co-lor-protecting.And color-protecting system mainly includes a mixing tank,diaphram metering pump,vavles.
Apple/Pear belt press juicer
The belt press juicer is specially used for extracting juice from apple or pear,The equipment adopts muti-stage folding bar and pneumatic roller to press,after the juice is pressed.it will be feed into the vibrating screen to filter the fruit pomace in juice.At the same time,it also has the characteristics of energy-saving,high degree of automation,automatic feeding and discharging,continuous work,strong universality,sufficient pressure and filtration,low water filtration of filter cake,convenient operation and maintenance,etc.The juice yield rate can reach 70%-90% with belt press,which can increase the yield rate of by 20-35% compared to other fruit juice extractors,so it can greatly reduce the production cost and improve the economic benefit of the enterprise.
Ultrafiltation system for clear apple juice
The Ultra-filtration system is designed to produce clear apple juice in the juice processing line.It is consist of tanks,recycling pump,membrane stack as the core part,clear juice pump,clear juice tank,and control system etc.This system has high filtration accuracy and less loss of effective nutrients and aromatic components in the juice.And the system process mature and reliable,high degree of automation,simple operation,high labor intensity.
Apple/Pear juice sterilizing machine
Clear apple juice uses tubular type or plate type sterilizer to process depending on the filling method.If we use the hot filling,then we can use the plate-type pasteurizer.The sterilizing technological process is 90-95℃ for 15 sec;if we use the aseptic filling,then we use the tubular type sterilizer.The sterilizing technological process is 135-137℃ for 4-6 seconds.
Apple/Pear juice filling machine
There are two types for filling,One is for the hot filling,the other is for aseptic filling.The hot filling machine usually connects with pasteurizer,filling into small bottles or pouches;And aseptic filling machine usually connects with tubular type UHT sterilizer,filling into aseptic bags,tetra pak packages.
Project samples
No. | Project information | Place | Remark |
1 | 5 t/H pear juice production line | Hebei Cangzhou | Turnkey project |
2 | 5 t/H apple vinegar production line | Shandong yantai longkou | Sterilization and after-filling equipments |
3 | 10 t/H fruit juice with fruit grain production line | Beijing | Turnkey project |
4 | Concentrated fruit juice production line |
Fujian Sanming |
Original fruit pre-process project |
5 | 12000 p/H wild papaya beverage production line | Guizhou zunyi | Turnkey project |
Machine list for apple juice concentrate production line
Flow No. |
Name |
Size |
Main technical parameter |
A.Fresh fruit washing and crushing system |
|||
A-1 |
Bubble cleaning machine with elevator |
3T/H |
SUS304, fruit washing pool, stainless steel baffle plates (the baffles are all with holes) are all made of SUS304, elevatoring speed is manually adjustable, with spray cleaning, the sloping bottom, hand hole, an overflow port, discharging port, the size is about, L*W*H=4500mm×1200mm×1200mm, the diameter of the baffle is, 2500mm×1000mm |
A-2 |
Roller sorting machine |
3T/H |
SUS304 support, with rollarounds (φ38×800mm) for sorting the fruits, and the speed is adjustable, and the size is about, L*W*H=3000mm×1200mm×1200mm |
A-3 |
Bubble cleaning machine with clapboard elevator |
3T/H |
SUS304, fruit washing tank, stainless steel clapboard plates (the baffles are all with holes) are all made of SUS304, elevatoring speed is manually adjustable, with spray cleaning, the sloping bottom, hand hole, an overflow port, discharging port, the size is about, L*W*H=4500mm×1200mm×1200mm, the clapboard elevating size is, 2500mm×1000mm |
A-4 |
Crusher |
3T/H |
|
A-5 |
Accessories adding unit |
100L/H |
The whole system include, accessories dissolving tank (SUS304, single layer, 100L, semi open cover, accessories tank, paddle agitator), dosing pump (0-100L/H, stepless adjustable, 6 Bar), 1/2'', and with 2 sprinkler heads |
A-6 |
Buffer tank |
500L |
SUS304, single layer, with ladder, adjustable feet, and cone type cover, with flange type outlet at the bottom, electrode type liquid level, digital temperature sensor. With CIP cleaning balls, inlets for pure water and material |
A-7 |
Screw pump |
3T/H |
The material contact parts are all food grade rubber, and the pressure of the outlet is 0.6MPa, frequency conversion speed regulation |
A-8 |
Tublar heater |
3T/H |
SUS304, one section, direct steam heating, and the difference of the material is 25-55℃ |
A-9 |
Platform for crusher |
|
Carbon steel support , anti slip stainless steel checkered plate, steps, guard bar, central drainage, L*W*H=2000mm×2000mm×2000mm |
B. Enzymolisys system |
|
||
B-1 |
Enzymolisys tank |
4000L |
SUS304, PU insullation, airtight manhole, cone type cover, and on the top has CIP cleaning balls, digital thermometer, sight glass level meter, adjustable feet, breathing valve, off-center vertical agitator, and tie valve at the bottom |
B-2 |
Rotor pump |
5T/H |
SUS304 stainless steel, and the pressure of the outlet is 0.6MPa |
B-3 |
Screw squeezer |
3T/H |
The main part of the equipment adopts SUS304, and the speed of the waste discharging is adjustable, frequency control |
B-4 |
Buffer tank |
500L |
SUS304, single layer, with ladder, adjustable feet, and cone type cover, with flange type outlet at the bottom, electrode type liquid level, digital temperature sensor, and products inlets and outlets |
B-5 |
Centrifugal pump |
5T/H |
SUS304, lift 24m, machinery seal |
B-6 |
Vibrating sieve |
3T/H |
SUS304, 100 mesh single-deck screen |
B-7 |
Collecting tank |
500L |
SUS304, circular type, open type, and with cone type outlet, single layer, with high-middle-low level indicator (floating ball type ), linkage with the discharge pump |
B-8 |
Centrifugal pump |
5T/H |
SUS304, lift 24m, machanical seal |
B-9 |
Sprial slag conveying machine |
1T/H |
SUS304, the diameter is 200mm, and the length is about 5000mm |
B-10 |
Platform of squeezer |
|
SUS304, anti slip stainless steel checkered plate, steps, guard bar, central drainage, L*W*H=3000mm×3500mm×2000mm |
C.Pasteurization and second-stage enzyme system |
|||
C-1 |
Temporary Storage tank |
3000L |
SUS304, PU insulation, airtight manhole, cone type cover, and on the top has CIP cleaning balls, digital thermometer, glass sight level meter, adjustable feet, breathing valve, off-center vertical agitator, and tie valve at the bottom |
C-2 |
Centrifugal pump |
10T/H |
SUS304, lift 24m, machanical seal |
C-3 |
Pasteurizer |
3T/H |
SUS 304, tubular type, PID auto control, material inlet temperature 40-50℃, 95℃, 30s, material outlet temperature 55℃, Spirax Sarco steam control system |
C-4 |
Enzymolisys tank |
4000L |
SUS304, PU insulation, airtight manhole, cone type cover, and on the top has CIP cleaning balls, digital thermometer, glass sight level meter, adjustable feet, breathing valve, off-center vertical agitator, and tie valve at the bottom |
C-5 |
Centrifugal pump |
5T/H |
SUS304, lift 24m, machanical seal |
C-6 |
Enzymolisys platform |
|
SUS304, anti slip stainless steel checkered plate, steps, guard bar, central drainage, L*W*H, 6800mm×800mm×1700mm |
D. Filtration and clarification system |
|||
D-1 |
Horizontal spiral separator |
3T/H |
Automatic deslagging, within the starting control cabinet, main and auxiliary motor are variable frequency adjustable |
D-2 |
Buffer tank |
500L |
SUS304, single layer, with ladder, adjustable feet, and cone type cover, with flange type outlet at the bottom, electrode type liquid level, digital thermometer, CIP cleaning balls and pure water and products inlets and outlets |
D-3 |
Centrifugal pump |
5T/H |
SUS304, lift 24m, machanical seal |
D-4 |
Screw conveyor for waste |
1T/H |
SUS304, the diameter is 200mm, and the length is about 5000mm |
D-5 |
Platform for separator |
|
SUS304, anti slip stainless steel checkered plate, steps, guard bar, central drainage,L*W*H=4000mm×4500mm×2000mm |
D-6 |
Cleaning water tank |
10000L |
SUS304, PU insulation, airtight manhole, cone type cover, ladders, digital thermometer,glass sight level meter, over flow vent, adjustable feet and tie valve at the bottom, inside coil heating |
D-7 |
Centrifugal pump |
10T/H |
SUS304, lift 24m, machanical seal |
D-8 |
Circulation tank |
5000L |
SUS304, PU insulation, airtight manhole, cone type cover, and on the top has CIP cleaning balls, digital thermometer, glass sight level meter, adjustable feet, breathing valve, off-center vertical agitator, and tie valve at the bottom |
D-9 |
Centrifugal pump |
10T/H |
SUS304, lift 24m, machanical seal |
D-10 |
Ultra-filter |
3T/H |
SUS304, with cleaning equipments, fully-automatic controlled, the main control parts all adopts international brand, with feeding pump |
D-11 |
Temporary storage tank |
3000L |
SUS304,singal layer tank, airtight manhole, cone type cover, and on the top has CIP cleaning balls, digital thermometer, glass sight level meter, adjustable feet, breathing valve |
D-12 |
Centrifugal pump |
10T/H |
SUS304, lift 24m, machanical seal |
E.Concentrating system |
|||
E-1 |
Double effect falling film evaporator |
2T/H |
Product contacting part material, SUS304, carbon steel support, evaporation self control, brix/temperature are all fully controlled, falling film evaporator, downstream type |
E-2 |
Product tank |
1000L |
SUS304,three layers, with dimple jacket, PU insulation, airtight manhole, cone type cover, and on the top has CIP cleaning balls, digital thermometer, glass sight level meter, adjustable feet, breathing valve, off-center vertical agitator, and tie valve at the bottom |
E-3 |
Rotor pump |
5T/H |
SUS304 stainless steel, outlet pressure is 0.6MPa |
F. Sterilization and juice filling system |
|||
F-1 |
Tubular UHT sterilizer |
Q=1T/h |
Tubular type, process flow parameter is 25~50℃——>115℃(15s) (sterilizing)——> 88℃ (hot filling),Spirax Sarco steam depressure valve, regulating valve, drain value, JUMO temperature sensor, Burkert tower water regulating valve, GEA/APV pneumatic valve, paperless temperature recorder, Simens PLC touch screen control, with self CIP cleaning system |
F-2 |
Vacuum degasser |
Q=1T/h |
SUS 304, water-ciruclation vacuum pump, vacuum degree -0.08Mpa, differential pressure sensor level control, vertical multistage centrifugal pump, variable frequency control |
F-3 |
Aseptic bag filling |
1T/h |
|
To customize a fully automated production line for apple sauce that meets your needs, we need to consider multiple factors, including production volume, raw material characteristics, product quality standards, budget, and special requirements. Here is a detailed customization process:
1. Requirement analysis
•
Production demand: Determine the daily or hourly production volume.
•
Raw material characteristics: Select suitable apple varieties and understand their characteristics such as moisture content, sugar content, and acidity.
•
Product quality standards: Clearly define the sensory, physicochemical, and microbiological indicators of the product.
•
Budget: Determine the overall budget of the project, including equipment procurement, installation and commissioning, operating costs, etc.
•
Special requirements: If there are special flavors, packaging forms, environmental requirements, etc., please inform us in advance.
2. Equipment selection
•
Raw material receiving and cleaning system: Select suitable conveyor belts, vibrating screens, high-pressure water guns, and cleaning tanks.
•
Peeling, Core Removal, and Slicer: Choose the appropriate peeling, core removal, and slicer for apples based on their size and shape.
•
Pre cooking and softening system: Choose an efficient pre cooking pot and steam generator.
•
Beating and filtering system: Choose high-performance pulping machines and filters.
•
Mixing and blending system: Select mixing tanks and mixers with appropriate capacity.
•
Sterilization and cooling system: Choose efficient pasteurizers and cooling tunnels.
•
Filling and sealing system: Choose the appropriate filling machine and sealing machine according to the packaging form.
•
Packaging and palletizing system: Choose automatic packaging machine and palletizing machine.
•
Quality inspection system: Select necessary testing instruments, such as pH meters, sugar meters, microbiological detectors, etc.
3. Process design
•
Process flow diagram: Draw a detailed process flow diagram, clarify the equipment layout and operation steps for each link.
•
Process parameters: Determine key process parameters for each stage, such as temperature, pressure, time, etc.
•
Automated control: Design an automated control system to achieve automation and intelligence in the production process.
4. Layout planning
•
Factory layout: Based on equipment size and process flow, plan the factory layout reasonably to ensure smooth production.
•
Logistics channel: Design a reasonable logistics channel to facilitate the transportation of raw materials and finished products.
•
Safety and hygiene: Ensure safety and hygiene during the production process, in compliance with relevant standards and regulations.
5. Installation and debugging
•
Equipment installation: Install and debug the equipment according to the design drawings and process requirements.
•
System integration: Connect various devices to form a complete production line.
•
Trial operation: Conduct a trial operation to check the performance of the equipment and the stability of the system.
6. Training and Support
•
Operation training: Provide equipment operation and maintenance training to operators.
•
Technical support: Provide long-term technical support and after-sales service to ensure the normal operation of the production line.
7. Continuous improvement
•
Feedback collection: Regularly collect feedback information during the production process, continuously optimize production processes and equipment performance.
•
Quality control: Establish a sound quality management system to ensure the continuous stability of products.